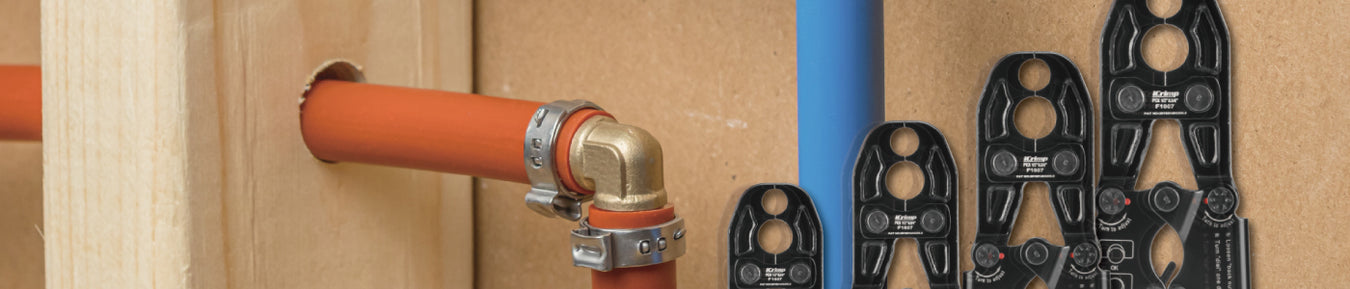
Pex Pipe Tools
Here is a list of common Pex pipe tools and their functions:
- PEX pipe cutter: It helps make a straight and clean cut of PEX pipes.
- PEX crimping tool: It’s used when making Pex connections to crimp PEX rings around PEX pipe and PEX fitting.
- PEX expansion tool: It’s a tool used to expand/enlarge the end of a PEX pipe and sleeve to allow the insertion of expansion-type fittings to make connections
- PEX pressing tool: It’s used to press PEX press fittings on PEX pipes to make secure connections.
- PEX cinch/clamping tool: It’s used to pinch the tab on the clamp ring when connecting the PEX pipe to crimp-style fittings.
-
IWS-FA F1807 All-in-one Copper Ring Crimping Tool Kit
Original Price $7.99 - Original Price $80.99Original Price$7.99 - $80.99$7.99 - $80.99Current Price $7.99| /Brand: IWISSColor: Red, BlueItem Weight: 5.71 PoundsItem Dimensions LxWxH: 6.69 x 1.97 x 1.57 inchesGrip Type: Ergonomic Capability: IWS-FA PEX Cr...
View full details -
Expsnion Head for ProPex Connection with Auto Rotate Mechanism
Original Price $21.59 - Original Price $59.39Original Price$21.59 - $59.39$21.59 - $59.39Current Price $21.59| /F1960 Expsnion Heads Set Includes: 1/2", 3/4", 1" three expansion heads, and one grease
-
IWS-PE1632 Europe standard PEX Pipes Tube Expander With 16/20/25/32mm Expansion Heads
Original Price $28.35 - Original Price $107.72Original Price$28.35 - $107.72$28.35 - $107.72Current Price $28.35| /IWISS PEX Pipes Tube Expander With 16/20/25/32mm Expansion Head Suits Uponor For Water And Radiator Connection The IWS-PE1632 Europe standard Pex ...
View full details -
CL 1/2" ASTM F1807 PEX Pipe Crimping Tool, for 1/2-inch Copper Pex Crimps Rings, with Go/No-Go Gauge, Angled Head
Original Price $39.99 - Original Price $39.99Original Price$39.99$39.99 - $39.99Current Price $39.99| /Brand: IWISSColor: OrangeHandle Material: PipingGrip Type: Ergonomic Meet ATSM F1807 Help you reach into tight connection and make the pipe instal...
View full details -
CRP650 Vertical&Parallel PEX SS Clamp Cinch Tool for 3/8” to 1”
Original Price $16.99 - Original Price $16.99Original Price$16.99$16.99 - $16.99Current Price $16.99| /Brand: iCRIMPColor: BlueHandle Material: Stainless SteelGrip Type: Ergonomic 「Universal」This cinch tool meets ASTM 2098 standard works with stainl...
View full details -
IWS-FAS F1807 PEX Crimping Tool Kit for 3/8 inch, 1/2 inch, 3/4 inch, 1 inch Pex Copper Crimp Rings, c/w PEX Cutter,Go-no-go Gauge
Original Price $7.99 - Original Price $47.99Original Price$7.99 - $47.99$7.99 - $47.99Current Price $7.99| /Brand: IWISSColor: OrangeItem Weight: 0.01 OuncesHandle Material: Hardened SteelGrip Type: Ergonomic Multi-Head PEX Crimper: IWS-FAS copper ring c...
View full details -
IWS-1234C KIT-1/2"&3/4" Angel Combo PEX Pipe Crimping Tool kit- Portable Case
Original Price $55.99 - Original Price $55.99Original Price$55.99$55.99 - $55.99Current Price $55.99| /Brand: IWISSItem Weight: 3.96 PoundsColor: orange, black, whiteGrip Type: Ergonomic All-in-One PEX Piping Tool Kit: IWS-1234C PEX plumbing kit i...
View full details -
IWS-1010R F1807 PEX Copper Ring Removal Tool for 1/2-Inch, 3/4-Inch, 1-Inch
Original Price $12.99 - Original Price $12.99Original Price$12.99$12.99 - $12.99Current Price $12.99| /This easy use and lightweight cutter can remove the crimped rings without damaging the fittings. Apply to pipe sizes 1/2", 3/4" and 1" Allows reus...
View full details -
IWS-1234W 1/2"&3/4" Angel Combo PEX Pipe Crimping Tool-Single Tool with Go/No-Go Crimp Gauge
Original Price $45.99 - Original Price $45.99Original Price$45.99$45.99 - $45.99Current Price $45.99| /Brand: IWISSColor: OrangeItem Weight: 2.05 PoundsHandle Material: Orange, blackGrip Type: Contoured 2-IN-1 PEX Crimping Tool: IWS-1234W PEX crimp ...
View full details -
IWS-F1960 1/2, 3/4 &1-inch PEX Pipe Expander Tool Kit for ProPex Fitting meet ASTM F1960
Original Price $36.75 - Original Price $90.99Original Price$36.75 - $90.99$36.75 - $90.99Current Price $36.75| /Brand: IWISSColor: SilverItem Dimensions LxWxH: 15.75 x 5.91 x 2.76 inches Purpose: IWS-1960 expander tool is designed for expanding type A PEX pi...
View full details -
IWS-S1234 1/2&3/4" ASTM 877 SS Sleeves Combo Crimping Tool
Original Price $30.99 - Original Price $30.99Original Price$30.99$30.99 - $30.99Current Price $30.99| /Meets ASTM F877 standard Well polished jaw brings two circular grooves with no damage to the sleeves Reasonable structural design makes the crimpi...
View full details -
IWS-1960R PEX Expansion Tool Kit, Sized 1/2,3/4,1-inch, Auto Rotation Expander Tool with Pex-A Tubing Installed for Uponor ProPEX, PowerPEX Expansion Ring
Original Price $125.99 - Original Price $125.99Original Price$125.99$125.99 - $125.99Current Price $125.99| /Material: PexBrand: IWISSColor: BlackConnector Type: Adapter Components: IWS-1960R PEX-a Expansion Tool Kit with 1/2 in., 3/4 in. and 1 in. expand...
View full details -
IWS-S12 1/2" ASTM F877 SS Sleeves Crimping Tool
Original Price $42.99 - Original Price $42.99Original Price$42.99$42.99 - $42.99Current Price $42.99| /Brand: IWISSColor: Blue,blackItem Weight: 0.01 OuncesHandle Material: Stainless SteelGrip Type: Ergonomic Meet ASTM F877 Standard Easy to use and ...
View full details -
IWS-1234PS 1/2" & 3/4" Combo Pex Pipe Copper Ring plumbing Tool with Gauge
Original Price $30.90 - Original Price $30.90Original Price$30.90$30.90 - $30.90Current Price $30.90| /Brand: IWISSColor: RedItem Weight: 1.2 KilogramsHandle Material: Alloy SteelGrip Type: Ergonomic Meet ASTM F1807 Standard, compatible with 1/2-inc...
View full details -
CL 1" ASTM F1807 PEX Pipe Crimping Tool, for 1-inch Copper Pex Crimps Rings, with Go/No-Go Gauge, Angled Head
Original Price $48.99 - Original Price $48.99Original Price$48.99$48.99 - $48.99Current Price $48.99| /Brand: IWISSColor: OrangeHandle Material: PipingGrip Type: Ergonomic Purpose: PEX-1 F1807 PEX Copper Crimp Ring Angle Tool is designed to secure 1...
View full details -
IWS-S34 3/4" ASTM 877 SS Sleeves Crimping Tool
Original Price $55.99 - Original Price $55.99Original Price$55.99$55.99 - $55.99Current Price $55.99| /Brand: IWISSColor: Blue,blackHandle Material: Stainless SteelGrip Type: Ergonomic Meet ASTM F877 Standard Easy to use and carry;Save Labor Made of...
View full details -
SL 1" ASTM 877 Angle SS Sleeves Crimping Tool
Original Price $61.99 - Original Price $61.99Original Price$61.99$61.99 - $61.99Current Price $61.99| /Features: Meets ASTM F877 standard, compatible with Viega PureFlow Press Constructed of high-quality steel with rust resistance surface tre...
View full details -
KIT-1960D Expanding Tool Kit with Auto-Rotate Expansion Heads for 3/8,1/2,3/4&1 in. F1960 system
Original Price $20.00 - Original Price $135.99Original Price$20.00 - $135.99$20.00 - $135.99Current Price $20.00| /Brand: IWISSColor: MulticolorConnector Type: RingExterior Finish: Brass KIT-1960D PEX-a Expansion Tool Kit includes 1 x Expander Tool, 3 x Expansi...
View full details -
IWS-1210C PEX Crimp Ring Removal Tool for 1/2-Inch,3/4-Inch,1-Inch F1807 Copper Crimp Rings
Original Price $14.99 - Original Price $14.99Original Price$14.99$14.99 - $14.99Current Price $14.99| /Brand: IWISSHandle Material: Alloy SteelGrip Type: Ergonomic Remove Tool Pex Ring Remove tool Ring Cutting Tool crimp ring removal tool copper rin...
View full details -
CRP-1096 ASTM2098 Ratchet PEX SS Clamp Cinch&Remove Tool for 3/8 to 1-inch
Original Price $18.99 - Original Price $18.99Original Price$18.99$18.99 - $18.99Current Price $18.99| /Brand: iCRIMPColor: Black, BlueHandle Material: Polyvinyl Chloride (PVC)Grip Type: Ergonomic 「UNIVERSAL」Thistool meets ASTM 2098 standard will wor...
View full details -
CRP0409 ASTM F2098 PEX SS Clamp Cinch Tool Kit for 3/8" - 1"
Original Price $17.00 - Original Price $17.00Original Price$17.00$17.00 - $17.00Current Price $17.00| /Material: Stainless SteelBrand: ICRIMPItem Dimensions LxWxH: 11 x 3.54 x 1 inchesColor: Blue&redStyle: Modern 「Universal」Works with stainless ...
View full details -
CL 3/4" ASTM F1807 PEX Pipe Crimping Tool, for 3/4-inch Copper Pex Crimps Rings, with Go/No-Go Gauge, Angled Head
Original Price $43.99 - Original Price $43.99Original Price$43.99$43.99 - $43.99Current Price $43.99| /Brand: IWISSColor: OrangeHandle Material: PipingGrip Type: Ergonomic Meet ATSM F1807 With high quality made of high carbon steel for long time usi...
View full details -
KG-1096 KIT PEX Pipe Clamp Cinch Tool Crimping Tool for Stainless Steel Clamps from 3/8-inch to 1-inch with 1/2-inch 20PCS and 3/4-inch 10PCS SS PEX Clamps
Original Price $18.99 - Original Price $18.99Original Price$18.99$18.99 - $18.99Current Price $18.99| /Brand: IWISSColor: RedItem Weight: 2.2 PoundsItem Dimensions LxWxH: 11 x 1 x 7 inchesHandle Material: Rubber Meet ASTM F2098 This cinch tool is un...
View full details -
KG-1096 PEX SS Ratchet Clamp Cinch Tool Meets ASTM F2098
Original Price $14.99 - Original Price $14.99Original Price$14.99$14.99 - $14.99Current Price $14.99| /Brand: IWISSColor: RedItem Weight: 0.01 OuncesHandle Material: Stainless SteelGrip Type: Contoured Meets ASTM F2098 standard Wire EDM cutting proc...
View full details